What Makes Stainless Steel ‘Stainless’?
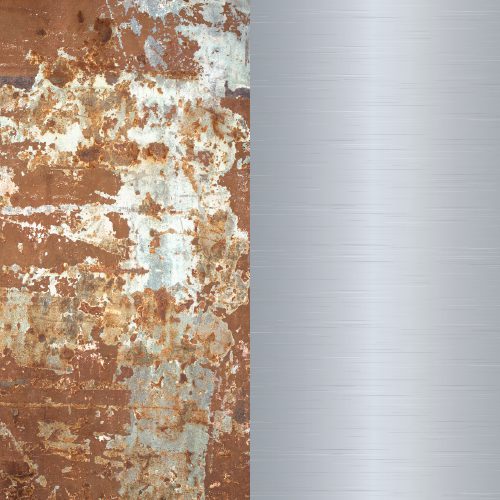
WHAT MAKES STAINLESS STEEL 'STAINLESS'?
Introduction to Stainless Steel
Stainless Steel is not just an alloy of iron, carbon and chromium, but also includes manganese and in certain classes, nickel and molybdenum, titanium, niobium as well. Despite its nefarious reputation, the layer that corrosion forms isn’t necessarily harmful. When aluminum corrodes, the resulting layer of aluminum oxide protects it from being further exposed to oxygen molecules and therefore prevents further corrosion! The same is true of chromium.
Stainless steel contains as much as 10% chromium, which reacts with the oxygen in the steel’s environment to form a hard, thin layer that protects the steel from corrosion by preventing the oxygen from seeping in any deeper and reacting with the iron in it. Although stainless steel is not as strong as other forms of steel, it is so resistant to rust that it can be easily used as a utensil or as a kitchen sink – objects that are perpetually in contact with water. It is also the chromium that gives these objects their characteristic polish or shine, making them constitutionally and in appearance, stainless!
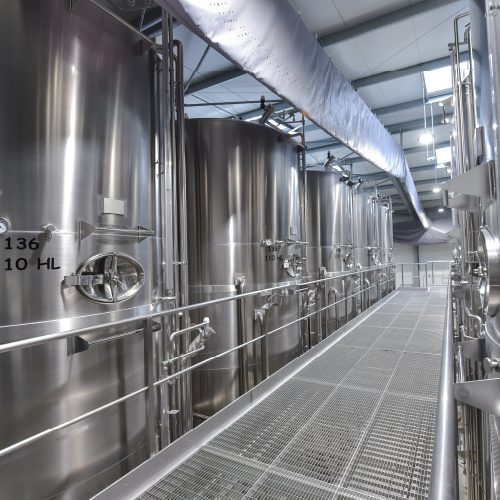
Introduction to Rust And Corrosion
The corrosion of iron causes a reddish-brown, rugged layer to form, which we call rust. Corrosion is simply the oxidation of a metal; when it reacts with oxygen, layers of metal oxides and hydroxides begin to form. Now, because oxygen is abundant in our environment, in air and water, a metal readily undergoes corrosion when exposed to them. When iron does this, we call the resulting iron-oxide layer “rust” and the process “rusting”.
The corrosion of iron is an electrochemical reaction, so the first layers of rust are only atoms thin, but prolonged exposure causes the layer to thicken and become increasingly conspicuous, such as the outgrowth on a wrench or on an old, abandoned car. Rust causes the iron to lose its strength and durability, so that eventually, a corroded wrench becomes no more useful than a paperweight. The global, annual losses due to rust are estimated to be in trillions of dollars, so not finding a way to deter it would have been foolish.
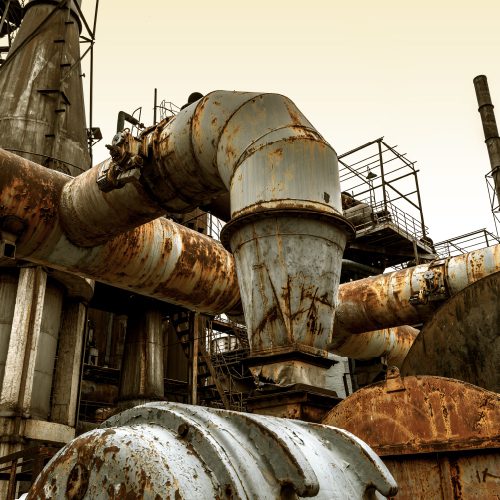
Introduction to Passivation
There is some dispute over whether the corrosion resistance of stainless steel can be enhanced by the process of passivation. Essentially, passivation is the removal of free iron from the surface of the steel. This is performed by immersing the steel in an oxidant, such as nitric acid or citric acid solution. Since the top layer of iron is removed, passivation diminishes surface discoloration.
While passivation does not affect the thickness or effectiveness of the passive layer, it is useful in producing a clean surface for further treatment, such as plating or painting. On the other hand, if the oxidant is incompletely removed from the steel, as sometimes happens in pieces with tight joints or corners, then crevice corrosion may result. Most research indicates that diminishing surface particle corrosion does not reduce susceptibility to pitting corrosion.
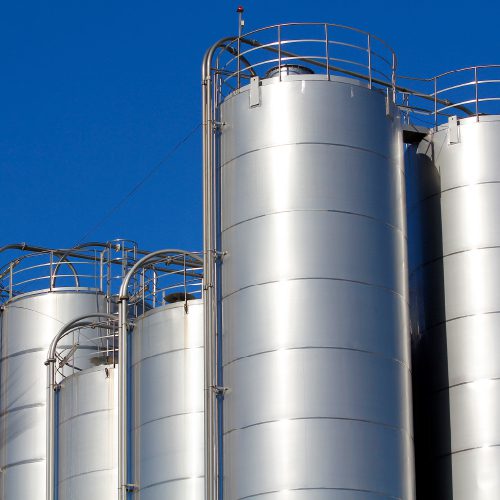
The Stainless Factor Of Stainless Steel
In technical terms, Stainless is explained as resistance to rust and corrosion over a period of time and under certain circumstances such as application and exposed enviornment. The alloying element Chromium is the primary factor to make the steel stainless: resistant to rusting. Even though Chromium is the primary factor responsible to 'Stainless' factor of the steel, the metal is often alloyed with other supporting elements like Nickel, Molybdenum and Manganese during manufacturing to enhance the properties of the steel. The elements are also added to ensure better performance of the steel under specific environment and circumstances.
The steel can be manipulated to increase toughness, ductility, formability, weldability, endurance, strength, hardness, heat-resistance and so many more factors. Each such enhanced stainless steel is categorised as grades for better organisation of the ever growing list. The categories of Stainless Steel grades are: Austenite, Ferrite, Martensite, Precipitation Hardening and Duplex. These materials can also have different finishes, which also affect the 'stainless' factor and life cycle of the material.
Popular grades of austenitic stainless steel include 301, 301LN, 303, 304, 304L, 316, 316L, 317L, 310S, 321 and 347 grades.
Common grades of ferritic stainless steel include 409, 409M, 430, 436, 441, 445, 439, and 444 grades.
Common duplex alloys include are 2202, 2205, 2304 and 2507 grades.
Some common martensitic stainless steel grades are 410, 410S and 420
Some common Precipitation Hardening grades are 15-5PH, 17-4PH and 17-7PH.
Stainless Steel: The Conclusion
With a wide variety of Stainless Steel Grades available to choose from, it becomes easier to find the perfect grade for each application as per their rust resistance properties under specific environment. Whether it be Automotive Exhaust or Automotive Grill, or Entrance of the Airport, there is a stainless steel grade to suit it all. The correct Stainless Steel Grade improves the product life cycle and lowers maintainance cost on ground level.
THANK YOU
DON'T MISS ON LATEST ARTICLES!
SIGN UP NOW!