Stainless Steel Welded Pipe Manufacturing Process
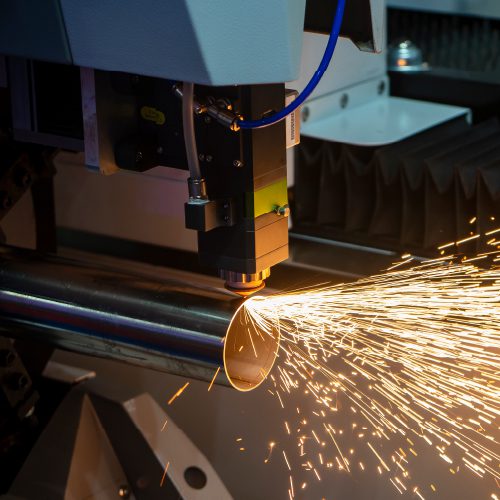
STAINLESS STEEL WELDED PIPE MANUFACTURING PROCESS
Introduction To Stainless Steel Welded Pipes
Stainless steel is one of the most popular, durable and versatile materials. Welded stainless steel pipes are mainly used in industrial transportation pipelines and mechanical structural parts such as petroleum, chemical industry, medical treatment, food, light industry, mechanical instrumentation, etc. In addition, when the bending and torsional strength are the same, the weight is light, so it is also widely used in the manufacture of mechanical parts and engineering structures.
Stainless steel alloys offer greater toughness, a higher work hardening rate, increased strength and hardness, greater ductility, and a more attractive appearance compared to carbon steel material. Stainless steel pipe is resistant to rust and other corrosive attack. It is also heat-resistant for high-performance and high-temperature use
Applications of Stainless Steel Welded Pipes
Stainless Steel Welded Pipes are used for all kind of applications where the medium is either liquid, air or semi-liquid. The long term benefits of using Stainless Steel pipes justify their cost as they do not require frequent maintainance and replacement in case of rusting or corrosion.
- Automotives
- Exhaust Systems
- Petrochemical Industry
- Furnace Tubes
- Fluid Transportation
- Utensils
- Food Industry
- Medical Equipements
- White Goods
The most commonly use Stainless Steel grades for Welded Pipes are 301, 304, 304L, 316, 316L, 316Ti, 310, 321, 2205, 2304, 904L, 409, 441, 439, 409M, 430, and many more
1) Electric Resistance Welding (ERW) Process
In Manufacturing of Stainless Steel Welded Pipes using Electric Resistance Welding (ERW) process, pipe is manufactured by cold-forming a flat sheet of steel into a cylindrical shape. Then current is passed between the two edges of the steel cylinder to heat the steel to a point at which the edges are forced together to form a bond without the use of welding filler material.
Several Electric Resistance Welding (ERW) processes are available for pipe production. The two main types of ERW are:
- High Frequency Welding
- Rotary Contact Wheel Welding
2) High Frequency Welding
Initially ERW manufacturing process used low frequency A.C. current to heat the edges. This low frequency process was used from the 1920’s until 1970. In 1970, the low frequency process was superseded by a high frequency ERW process which produced a higher quality weld. Over time, the welds of low frequency ERW pipe was found to be susceptible to selective seam corrosion, hook cracks, and inadequate bonding of the seams, so low frequency ERW is no longer used to manufacture pipe. The high frequency ERW process is still being used in pipe manufacturing.
There are two types of High Frequency ERW processes.
- High Frequency Induction Welding
- High Frequency Contact Welding
In High Frequency Induction Welding, the weld current is transmitted to the material through a work coil in front of the weld point. The work coil does not contact the pipe. The electrical current is induced into the pipe material through magnetic fields that surround the pipe. High frequency induction welding eliminates contact marks and reduces the setup required when changing pipe size.
In High Frequency Contact Welding, the weld current is transmitted to the material through contacts that ride on the strip. The weld power is applied directly to the pipe, which makes this process more electrically efficient than high frequency induction welding. Because it is more efficient, it is well-suited to large diameter and high wall thickness pipe production.
3) Rotary Contact Wheel Welding
In Rotary Contact Wheel Welding, the electrical current is transmitted through a contact wheel at the weld point. The contact wheel also applies some of the forge pressure necessary for the welding process. The three main types of rotary contact wheel welders are AC, DC, and square wave. In all three power supplies, electrical current is transferred by brush assemblies that engage slip rings attached to a rotating shaft that supports the contact wheels. These contact wheels transfer the current to the strip edges.
4) Submerged Arc Welding (SAW) Process
Submerged Arc Welding (SAW) process involves formation of an arc between a continuously fed bare wire electrode and the work-piece. The process uses a flux to generate protective gases and slag, and to add alloying elements to the weld pool. A shielding gas is not required. The arc moves along the joint line and as it does so, excess flux is recycled via a hopper. Remaining fused slag layers can be easily removed after welding. As the arc is completely covered by the flux layer, it is not normally visible during welding and heat loss is also extremely low. This produces a thermal efficiency as high as 60% (compared with 25% for manual metal arc.
There are two types of Submerged Arc Welding (SAW) processes:
- Longitudinal Submerged Arc Welding (LSAW) Process
- Spiral Submerged Arc Welding (SSAW) Process
5) Longitudinal Submerged Arc Welding (LSAW) Process
In Longitudinal Submerged Arc Welding (LSAW) Process, longitudinal edges of steel plates are first beveled using carbide milling equipment. Beveled plates are then formed into a U shape using a U-press and subsequently into an O shape using an O-press. Longitudinal edges of the plates are then tack welded followed by internal and external welds.
Pipes manufactured by this process are subjected to expanding operation in order to relieve internal stresses and obtain a perfect dimensional tolerance. After the pipes are conveyed to cold expansion, hydrostatic testing and NDT inspection, the pipes will be subject to final inspection. Good performances on high pressure resistance, and low-temperature corrosion resistance.
6) Spiral Submerged Arc Welding (SSAW) Process
In Spiral Submerged Arc Welding (SSAW) Process, also known as HSAW pipe, welding line shape like a helix. It is using the same welding technology of Submerged Arc Welding with LSAW pipe. Only major difference being SSAW pipe is spiral welded whereas the LSAW is longitudinally welded. Manufacturing process is rolling the steel strip, to make the rolling direction have an angle with the direction of the pipe center, forming and welding, so the welding seam is in a spiral line.
The SSAW pipe diameter range is from 20 inch (406 mm) to 100 inch (2540 mm).The advantage part is we can get the different diameter of SSAW pipes with the same size of the steel strip, there is a wide application for the raw material steel strip, and welding seam should avoid the primary stress, good performances to bear the stress. The disadvantage is the bad physical dimension, welding seam length is longer than the pipe length, easy to cause the defects of cracks, air hole, cinder inclusion, partial welding, welding force in pulling status.
7) Electric Flash Welding Process
In Electric Flash welding Process, a steel sheet is formed into a cylindrical shape. The edges were heated until they turn semi-molten and then forced together until molten steel was forced out of the joint and formed a bead. The seams of electric flash welded pipe are susceptible to corrosion and hook cracks. This type of pipe is also susceptible to failures due to hard spots in the plate steel occurred due to accidental quenching of the steel during the manufacturing process.
Electric Flash Welding is no longer used as a major process for pipe manufacturing.
8) Lap Welding Process
In Lap Welding Process, steel was heated in a furnace and then rolled into the shape of a cylinder. The edges of the steel plate were then “scarfed”. Scarfing involves overlaying the inner edge of the steel plate, and the tapered edge of the opposite side of the plate. The seam was then welded using a welding ball, and the heated pipe was passed between rollers which forced the seam together to create a bond. The welds produced by lap welding are not as reliable as those created using more modern methods.
Lap Welding is no longer used as a major process for pipe manufacturing.
Stainless Steel Welded Pipe Manufacturing Process: The Conclusion
Stainless Steel Welded Pipes have a wide range of manufacturing methods. The most of mentioned methods are widely adopted and do not compromise the quality of the pipes. Whereas some methods are no longer used for commercial purpose because of better quality methods are discoverd. Raykam Alloys ensure that each pipe is inspected and adhere to the quality checkmarks of the required standard. The Stainless Steel Welded Pipes are more econmonical than seamless pipes but they provide lower Tensile Strength and Corrosion Resistance than the seamless pipes. For non-critial uses, Welded Pipes are the first preference for their economic cost factor.
THANK YOU
DON'T MISS ON LATEST ARTICLES!
SIGN UP NOW!